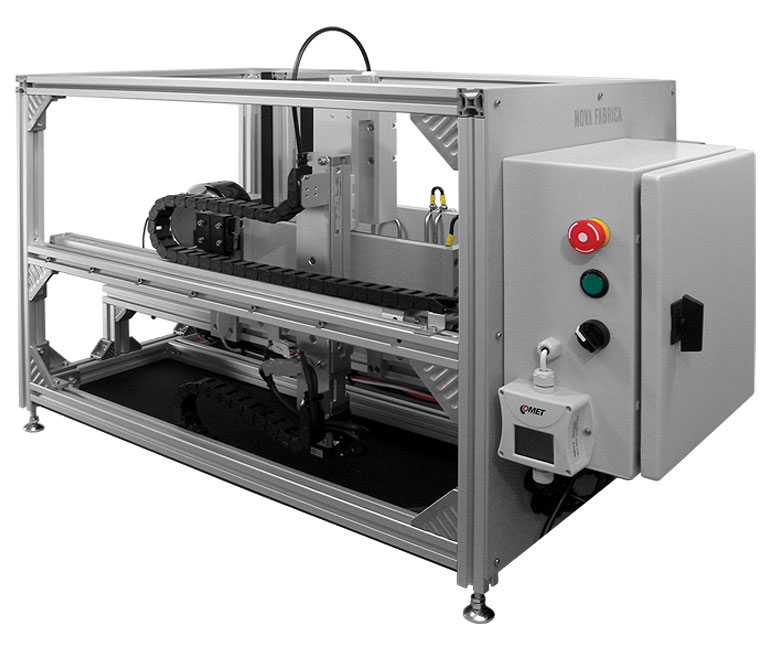
TECHNOLOGY
- Plasma electrolytic oxidation (PEO), also known as microarc oxidation (MAO), is an electrochemical surface treatment process for generating oxide coatings on metals. It employs higher potentials than anodising processes so that discharges occur, and the resulting plasma modifies the structure of the growing oxide layer. Thick (tens or hundreds of micrometres), largely crystalline, oxide coatings on metals such as aluminium, magnesium and titanium can be grown this way. The high hardness and continuous barrier produced by these coatings offer protection against wear, corrosion or heat and electrical insulation.
- OES is rapid, precise and sensitive to small process changes, thus an ideal tool to characterise PEO/MAO processes.
- OES is typically practised in the 200 to 1040 nm range with spectrometer resolution of 0.1 to 6.0 nm, the range and resolution being application-dependent.
- OES enables to determine what elements are present in the plasma by collecting the emitted light and analysing its spectrum in the UV-VIS-nIR range.
- OES enables process engineers to monitor the plasma process and detect events of critical importance. OES yields valuable process data that can be used for quality control in manufacturing and creating digital twins for simulation and testing.
HOW WE APPLY IT
We use spectral analysis of plasma discharges during Plasma Electrolytic Oxidation (PEO) and Microarc Oxidation (MAO) electrochemical surface treatment as a critical technological process development method. The properties of plasmas generated during PEO and MAO processes are related intimately to the structure and properties of the oxide layers produced. Thus, it is of paramount importance to be able to monitor, characterise and control PEO and MAO discharges accurately.
CHALLENGE
Surface treatment technologies are becoming increasingly complex as performance and environmental requirements change. You develop new materials and engineer surfaces to address the current needs. You cannot characterise the PEO/MAO process or find it hard to repeat the process condition, determine process drift, detect an abnormal process and prevent waste. Enhancing your process monitoring and control capabilities is critical to increasing product value, yield and reducing the overall ownership cost.
SOLUTION
Nova Fabrica’s turn-key solution, the Scanning 2B-PEM® system enables high-resolution OESbased monitoring, characterisation and feedback control of PEO and MAO discharges. The system is developed and tailored specifically for research and development of Plasma Electrolytic Oxidation and Microarc Oxidation processes. The system is comprised of an Inteleg® 2B-PEM® HR system, immersible corrosion resistant optical monitoring assembly, a certified calibrated uniform light source, precision X-Y scanner, 8-litre process electrolyte tank, electrolyte circulation system, 5 cm O.D. sample holders for vertical and horizontal placement, high-voltage power terminals, water cooling interfaces, humidity and temperature monitoring.
BENEFITS
- UV-VIS-NIR 2B-PEM® detector
- 300 to 850 nm detector range
- 0.2 nm optical resolution
- Immersible corrosion resistant optical assembly
- Integrated Uniform Light Source for calibration
- Precision X-Y scanner
- ±0.02 mm repetitive positioning accuracy
- 0.01 mm minimum travel amount
- 8-litre process electrolyte tank
- Electrolyte circulation system
- Vertical and horizontal sample holders
- Power terminals and water cooling interfaces
- Humidity and temperature monitoring